By Norihiko Shirouzu and Giulio Piovaccari
AUSTIN, Texas (Reuters) – Tesla has backed away from an ambitious plan for innovations in gigacasting, its pioneering manufacturing process, according to two sources familiar with the matter, in another sign that the electric-vehicle maker is retrenching amid falling sales and rising competition.
Tesla has been a leader in gigacasting, a cutting-edge technique that uses huge presses with thousands of tons of clamping pressure to die-cast large sections of the car’s underbody. On a typical vehicle, the underbody can consist of hundreds of individual parts.
Last year, as Tesla developed a new small-vehicle platform, it aimed to punch out the underbody in a single piece, Reuters exclusively reported last September, citing five sources familiar with the automaker’s gigacasting operations. The long-term goal was to radically simplify manufacturing and slash costs.
But Tesla has since halted the effort, opting to stick with its more proven method of casting vehicle underbodies in three pieces: two gigacasted front and rear sections and a midsection made of aluminum and steel frames to store batteries, according to the two sources familiar with the matter. That is largely the same three-piece method the company has used for its last two new models, the Model Y crossover SUV and the Cybertruck pickup.
Tesla’s retreat from one-piece gigacasting has not been previously reported. The automaker did not respond to a request for comment.
The decision to hold off on the potential manufacturing breakthrough marks another example of Tesla slashing short-term spending as it adjusts to falling sales and profit margins, softening EV demand globally, and intensifying competition from rival EV makers such as China’s BYD. Tesla last month laid off more than 10% of its global workforce. A handful of senior executives have also resigned or been pushed out.
Such moves also reflect a fundamental strategy shift, with Tesla now focusing more on developing self-driving vehicles than on pushing for huge growth in EV sales volume, which many investors had been counting on.
The step-back on gigacasting occurred last autumn, the people said, before Tesla decided in late February to halt development of an all-new affordable car, often called the Model 2, which would have been the first vehicle it built with one-piece gigacasting. Reuters first reported the cancellation of the Model 2 on April 5.
On April 23, as it released earnings that missed Wall Street expectations, Tesla said it had a simpler, faster plan for producing “more affordable” cars after shelving plans for the Model 2, which was expected to cost $25,000 and be released in the second half of 2025.
Instead, Tesla officials said, it would produce affordable models using a current platform and production lines. On an investor call, Chief Executive Elon Musk declined to provide details on the planned new offerings or their target prices.
Tesla has not entirely abandoned the small-vehicle platform it had planned for the Model 2. Instead, it will move forward in developing a self-driving robotaxi on the same platform, Reuters reported in the April 5 story. One of the two sources familiar with the automaker’s gigacasting operations said the suppliers involved are now adapting Tesla’s three-piece process for the next-generation vehicle.
Both sources said the automaker decided last autumn to halt work on the more innovative and difficult one-piece casting process. At the time, the rationale for the decision was to speed development of the now-defunct Model 2 and avoid any costly delays or manufacturing problems, the two sources said.
BIG UPFRONT INVESTMENT
Tesla and Musk have said gigacasting helps the automaker reduce costs over the long term. But the process requires large initial investments and is difficult and time-consuming to perfect, automotive manufacturing experts say.
Experts in vehicle manufacturing said Tesla’s more conservative path on gigacasting is no surprise and in part reflects the pains it has experienced historically in launching complex and innovative vehicles on time. The automaker’s highly experimental Cybertruck arrived last autumn at a far higher price than predicted after substantial delays to work through manufacturing issues. Tesla is still struggling to produce the angular, stainless-steel pickup in mass-market volumes.
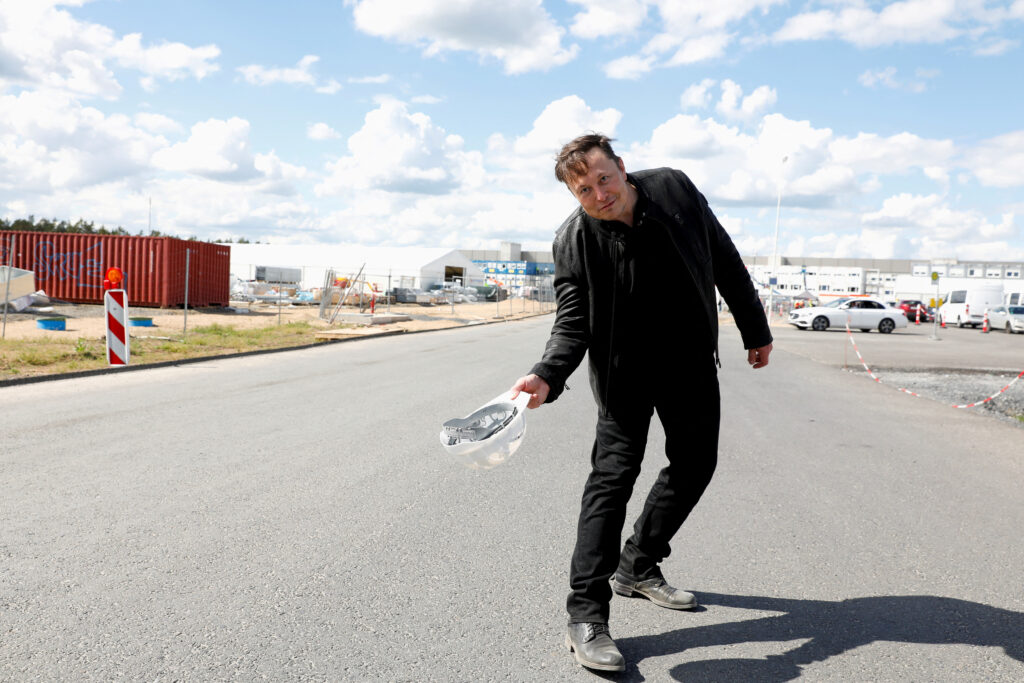
Holding off on one-piece gigacasting will save the company from making massive short-term capital investments in manufacturing and design, said Terry Woychowski, president of U.S. engineering company Caresoft Global, who has led teardowns and engineering analyses on numerous vehicles, including Teslas.
“Would they rather have done it all in one big piece? Sure, they would’ve, but at what cost?” Woychowski asked.
James Womack, a vehicle manufacturing expert and former research director at the Massachusetts Institute of Technology, said Tesla’s gigacasting pullback reflects the company’s scramble last year to launch an all-new $25,000 car to catch up with Chinese EV makers who are already dominating the low-cost EV segment.
But pushing forward with an innovative production technique would do little to help sell a Tesla car to consumers, Womack said.
“It’s not very exciting from the standpoint of the public and buyer,” Womack said, “and you don’t know whether this is really a big cost-saver or not.”