Wearable devices are more spotted often around us than before, and so are e-textiles. E-textiles, or electronic textiles, are fabrics that have electronic components, for example, batteries or controllers embedded. Different from smart textiles, general fabrics applied with new technologies, e-textiles do not need extra installations of devices to use, as they are conductive.
Despite the versatile uses of e-textiles, manufacturing them has been rather complex. One of the most common ways is to coat fabrics with conductive ink and weave them with general fabrics. Another way is to add a functional layer onto general fabrics. Not only these conventional manufacturing methods were complicated, but they also allowed less flexibility in design. In addition, these methods were complex to deploy in mass production as they were not completely free from health risks, such as leakage of harmful chemicals. Understanding this pain point, a team of researchers based in South Korea found a much simpler way to make e-textiles: irradiating laser onto fabrics’ surfaces.
‘Conductive laser-induced graphene e-textiles’
Researcher Kwon Soon-geun of the Department of Nano Manufacturing Technology of the Korea Institute of Machinery and Materials, which is under the South Korean Ministry of Science and ICT, and Professor Kim Young-jin of the Department of Mechanical Engineering of the Korea Advanced Institute of Science and Engineering led the joint study team to introduce an easier technology to make e-textiles in August 2023.
According to their method, the conductivity of e-textiles can be realised through the application of femtosecond laser processing technology. The femtosecond laser processing technology means a material processing method with ultrafast laser with shorter pulse widths and higher power. The technology does almost no damage to processing materials compared to commonly used laser technologies, which is why it is good for micropatterning.
The researchers converted Kevlar textiles to conductive laser-induced graphene (LIG) by irradiating high-power laser (femtosecond laser pulses in ambient air) to surfaces in ambient air. When the laser reaches the parts of fabrics, the light energy changes into thermal energy on the surface, fabricating a carbon material on the details. Since the material’s structure is like graphene — a two-dimensional nanomaterial — it is named LIG. After the laser process, the parts showed a high level of conductivity and chemical reliability, with a low sheet resistance. The team explained that this is the world’s first multimodal graphene-based e-textiles used for customisable e-textiles. Multimodal refers to the process where sensory interfaces, like visual or auditory sensations, exchange information.
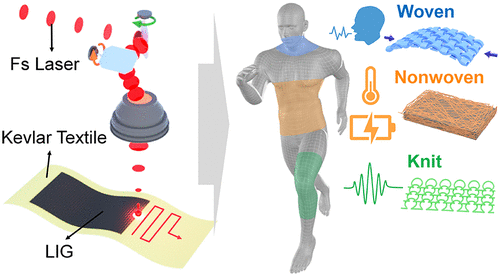
Simpler process, wider Use
The research team said that the process allows manufacturers to produce high-quality LIG fabrics by directing lasers onto fabrics’ surfaces, which is a far simpler process than conventional methods. Through this laser direct patterning technology, the surfaces of materials exposed to laser pulses are converted conductive without emitting toxic chemicals or waste. It also does not require optical masks. Alongside its easier manufacturing process, the technology’s other advantage is that it can be environmentally friendly as it does not need chemicals or extra processing.
Moreover, their laser patterning technology can allow more customisation depending on the structures of the fabrics they are irradiating. Multimodal e-textile components can be irradiated to various types of Kevlar textiles through the technology, including, but not limited to, nonwoven, knit, and woven structures. Each fabric carries different proponents and characteristics. For example, nonwoven textile is found to have high mechanical stability, which can be helpful for temperature sensors and micro-supercapacitors. The knit fabric can be used in making strain sensors to detect human motions with its stretchability. The woven textile may be suitable for making bendable sensors, often used for human voice detection, as it has pressure-sensing networks between parts of warp and weft.
The technology’s simpler manufacturing process may be helpful for mass production, like making commercial clothes or military items for personal healthcare. Moreover, it can be used in the health industry to create more customisable smart clothes.
Kwon, the principal researcher of this study, was quoted as saying in the team’s press release: “This technology has been developed by analysing the structures of generic fabrics and realising them as graphene-based materials that have advanced features of optimal e-textiles.” He added, “This technology is significantly meaningful in that it allows for the mass production of customised e-textiles using an environment-friendly and simple method.”