Electronics-Cooling Microchip – Sophisticated Device Cooling System that Mimics Human Capillaries
For decades, researchers have boosted the power of computers and other electronic devices by squeezing more and more transistors on each chip. These newly added components give off heat as they carry out their tasks. But as technology advances, the electronics get steadily smaller and denser. This means they also get hotter, which is why components often malfunction at high temperatures.
Dealing with the escalating heat that flows through the semiconductors of these shrieking items is a daunting technological challenge. There are various methods used to cool-off components, ranging from fan-cooled heat exchanges to more compact and sophisticated systems.
To effectively combat the heating problem in smaller devices, researchers have developed a liquid cooling system integrated directly within a microchip. It dramatically outperforms any of the previous approaches.
What is the new electronics-cooling microchip?
Scientists at the Swiss Federal Institute of Technology have developed a new technology to make electronic devices more energy-efficient. The new microchip has a micro-channel network built within the semiconductor itself, not attached to it afterward.
The design mimics and is heavily inspired by the human circulatory system. As study leader Elison Matioli explained: “It’s like the human circulatory system, which is made of larger blood vessels that only get thinner, transforming into capillaries, in certain areas of the body.”
Most chips today are cooled by using thermal materials to transfer heat from components to a large metal heat sink that dissipates the energy to the air, possibly with the help of a fan. This proved to be highly inefficient, as overheating is still a major problem for most electronics. Using liquid to cool chips is much more efficient, but most of the designs have failed so far because the cooling systems were added as an afterthought.
The key to this new approach is to create and embed the cooling system on the chip from the start in order to maximize the heat transfer.
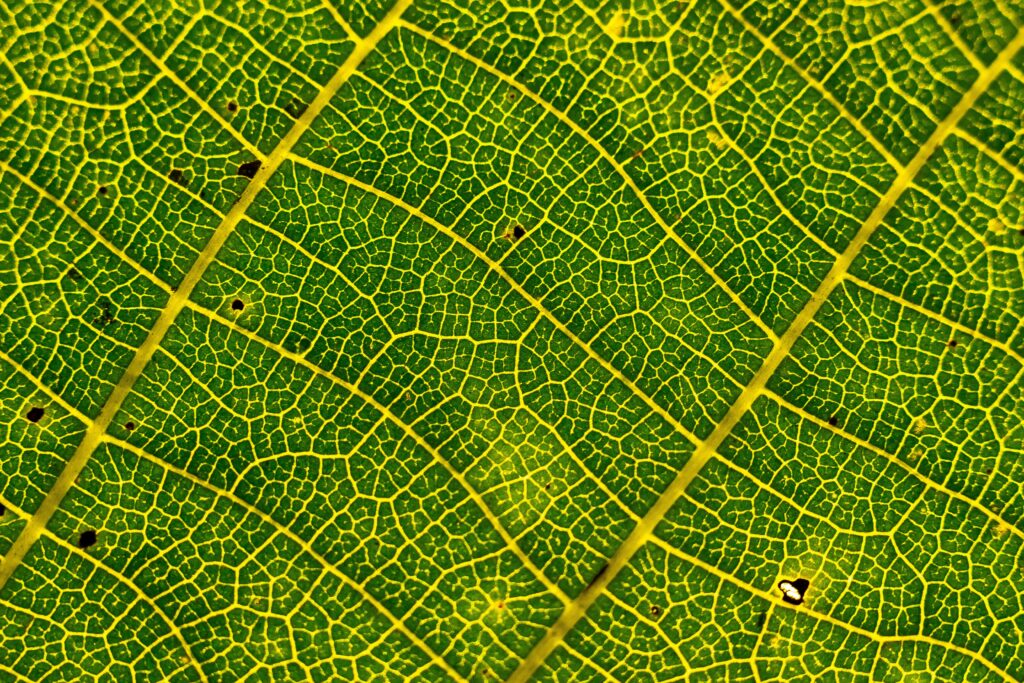
Photo by Samuel-Elias Nadler on Unsplash
How does it work?
Ordinary chips are made of a thin layer of a semiconducting material called gallium nitrite, which is supported by a thicker silicon substrate.
The new chip has micro-channels carved within the silicon substrate and positioned to line up exactly with the parts of the chip that tend to heat the most. Therefore, the heat is extracted exactly in the right place to prevent spreading throughout the device.
The approach relies on an innovative fabrication method that integrates electronic and cooling structures in a single manufacturing process.
To demonstrate the effectiveness of the system, they built a circuit that can convert AC current to DC current. After a series of testing, they have shown that the chip can easily cope with heat fluxes of 1,700 watts per square centimeter. Normally this kind of circuit would require a much bigger heat sink, but the team was able to squeeze it onto a USB-sized piece of circuit board.
The system is cooled with a water flow of less than a millimeter per second. Other experiments have shown the system’s efficiency to be 50 times higher than what was achieved with another cooling technology that is not integrated within the semiconductor.
Chip limitations
Despite the innovative and breakthrough technology, researchers have only implemented their approach on power electronics devices. These are responsible for controlling and converting electricity and are quite different from data-processing circuits found in computers, tablets, and mobile devices. Replicating this approach to different kinds of chips will be quite a challenge.
Some scientists have pointed out that aligning the coolant channels with all the components in a much more complex chip would be very tricky. Likewise, there is a concern that liquid going through the channels underneath the devices could lead to stress that may impact the device itself.
Still, this technology is promising, and as the concept matures, it could be used for all types of electronics in the future.